industrial robotsare important equipment in the upgrading of advanced manufacturing, and they are also an important indicator of the technological level of a country's manufacturing industry. The robot industry with industrial robots as the main body is an important way to solve the problems of rising industrial costs and environmental constraints in my country. an industrial robot is a multi-joint manipulator or a multi-degree-of-freedom machine device oriented to the industrial field. it can automatically perform work and is a machine that relies on its own power and control capabilities to achieve various functions. it can be commanded by humans, and it can also be run in accordance with pre-arranged programs. modern industrial robots can also perform tasks in accordance with principles and guidelines established by artificial intelligence technology.
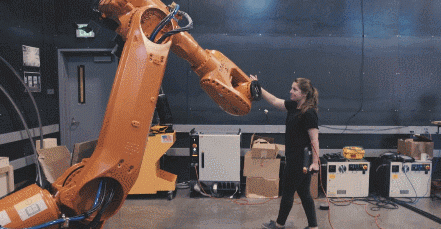
The first industrial robot conforming to the ISO standard was produced by bill griffith taylor in 1937 and published in meccano magazine in march 1938. This crane-like industrial robot is made of meccano parts and powered by a single electric motor. This industrial robot can stack wooden blocks in a pre-programmed way.
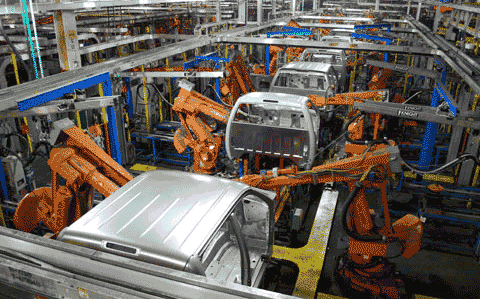
The middle of the 20th century was a critical period for the research and development of industrial robots. especially in the industrial environment, the work of repetitive motion and lifting heavy objects made the machine a great help to humans. most industrial robots are used in work environments that are too dirty, tiring, or dangerous for humans.
george Devol first proposed the concept of industrial robots, and applied for a patent in 1954 (patent approved in 1961). in 1956, Davor and joseph Engelberg jointly established Unimation based on Davor's original patent. in 1959, Unimation's first industrial robot was born in the united States, opening a new era of robot development.
▲ george Davor
robotics is a multidisciplinary field that combines the fields of mechanics, electronics, computer science, control, artificial intelligence, physics and mathematics. industrial robots are composed of six basic components: dynamic units, end-of-arm machines, digital computer controllers, actuators, input devices and detectors.
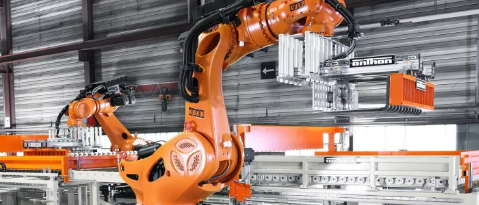
industrial robot actuator: The actuator controls each axis and maintains the direction of movement. Since the robot needs to handle the weight of various components, its motion varies greatly. send commands about the direction of movement from the robot computer and constantly check the feedback to ensure that the moving parts follow the correct route. This process requires high-speed equipment to send commands and read the movement of the system at a reasonable speed.
digital computer controller: For the robot, it controls the normal operation of each component. The computer controller can input and store various programs to determine the connection and relationship of the work sequence.
Sensors: The robot uses sensors to recognize and evaluate position changes, style differences, and obstacles or malfunctions of external systems.
feedback system: The feedback device of the industrial robot can measure the position, movement speed and acceleration of each axis. The axis must set any point to zero as a reference point in order to achieve relatively linear motion.
dynamic system: the motion part of the robot system including the industrial robot arm. The structure of the dynamic system is realized by connecting many rotation or linear motion joints.
The motion provided by industrial robot joints can place the robot structure or robot arm in a specific position. The different types of joint configurations are listed below——
▲ abb industrial robot completed the "Fanta Tank" challenge
articulated configuration: The articulated arm is the most common robot arm, very similar to a human arm. usually six-axis machines, they provide redundancy and move smoother.
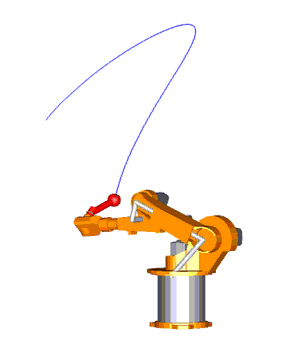
▲ articulated joint configuration
there are six rotary joints in the articulated configuration system, and each rotary joint is placed on the previous joint. They have a variety of configurations to reach a point within the working envelope or the ability to place equipment anywhere.
SCARA configuration: This four-axis arm mainly performs assembly tasks. They are small in size, but have the greatest carrying capacity.
▲ SCARA configuration joint configuration
The four-axis arm of the SCARA configuration is composed of basic rotation, linear vertical movement and two rotational movements. The linear vertical movement is in the same vertical plane. The four-axis arm of the SCARA configuration is very rigid in the vertical direction and can be ensured to be consistent with the horizontal plane.
cartesian configuration: cartesian robots are simple three axis robotsthat only contain linear drives with three spindles. usually used for picking and placing, handling, palletizing, plastic molding, assembly and machine maintenance.
parallel configuration: one of the new design developments is the parallel or incremental robot configuration, as shown in the figure below——
▲ parallel industrial robot
a parallel mechanism can be defined as a closed-loop mechanism in which the moving platform and the fixed platform are connected by at least two independent kinematic chains, the mechanism has two or more degrees of freedom, and is driven in parallel.
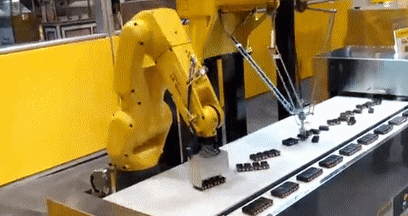
typical applications of industrial robots include welding, painting, assembly, collection and placement (such as packaging, palletizing and SMT), product inspection and testing, etc.; all tasks are completed with high efficiency, durability, speed and accuracy.
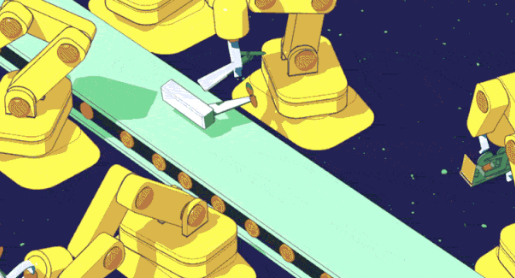
in order to perform work tasks more accurately, industrial robots usually include machine vision subsystems as their vision sensors, connected to powerful computers or controllers. For modern industrial robots, artificial intelligence robotshave become increasingly important equipment.